Polypropylene and polyethylene are two fascinating forms of plastic with their own unique properties and applications.
Polypropylene, also known as polypropene, is a versatile form of plastic that has distinct properties and applications compared to polyethylene. While both materials are widely used, polypropylene offers advantages such as moldability, high melting point, and resistance to fatigue.
Tired of reading? Watch the video here!
Polypropylene's ability to be molded and return to a solid state when cooled makes it pliable and suitable for structural and fiber applications. It can even be combined with rubber for enhanced flexibility Unlike polyethylene, it can withstand repeated motions and function as a hinge without fatigue. Additionally, polypropylene can be combined with other materials, such as rubber, to increase its flexibility.
Synthetic Paper: A Remarkable Application: One exciting use of polypropylene is in the production of synthetic paper by adding minerals. This synthetic paper is durable, tear-resistant, and water-resistant, allowing it to be used for various applications like banners, membership cards, maps, signs, and more. Synthetic paper offers the advantages of easy printing, folding, hot stamping, die-cutting, sewing, and environmental friendliness.
Applications in Automotive and Packaging Industries: Polypropylene finds extensive use in the automotive and packaging industries. The packaging sector alone accounts for 70% of polypropylene usage, with applications ranging from bottles and food containers to crates and pallets. It is also used in the manufacturing of housewares, appliances, toys, carpets, upholstery, and fibers for textiles.
Polyethylene: Unique Advantages: Polyethylene, on the other hand, has its own advantages. It is inert, creating lower static charges compared to polypropylene, making it suitable for housing collectible documents. Being translucent, it allows less light transmission than polypropylene. Polyethylene's lower static charge also attracts less dust and dirt. However, it tends to cost more due to its higher purity.
Here are some key differences between polyethylene and polypropylene:
Polyethylene can be produced optically clear, while polypropylene is translucent.
Polyethylene Optically Clear Example: Plastic Bags - High-quality, transparent plastic bags made from polyethylene allow users to easily view the contents without compromising their clarity. These bags are commonly used for packaging and storage purposes, providing a clear and visible solution.
Polypropylene Translucent Example: Storage Containers - Translucent polypropylene storage containers offer a balance between visibility and privacy. These containers allow users to get a glimpse of the contents inside, making it easier to identify and locate items, while also providing a degree of opacity for a neat and organized appearance.
Polyethylene performs better in cold temperatures and is a good electrical insulator but can become electrostatically charged (this can be mitigated with additives).
The temperature range for polyethylene varies depending on the specific type of polyethylene and its intended application. However, as a general guideline, polyethylene can typically withstand temperatures ranging from -50°C to 80°C (-58°F to 176°F). It is important to note that the temperature limits may vary for different grades and formulations of polyethylene, so it is always recommended to consult the manufacturer's specifications or technical data sheets for precise temperature ranges applicable to a particular polyethylene product or application.
Polypropylene is lighter, has higher resistance to cracking, acids, solvents, and electrolytes, and exhibits higher melting points and better dielectric properties.
Here are some examples:
-
Acids: Polypropylene has high resistance to a wide range of acids, including sulfuric acid (H2SO4), hydrochloric acid (HCl), nitric acid (HNO3), acetic acid (CH3COOH), and phosphoric acid (H3PO4). It maintains its structural integrity and chemical stability when exposed to these acidic substances.
-
Solvents: Polypropylene demonstrates good resistance to many organic solvents, such as benzene, toluene, xylene, acetone, methanol, ethanol, and mineral spirits. It can withstand prolonged exposure to these solvents without significant degradation or loss of mechanical properties.
-
Melting Point: The melting point of polypropylene typically ranges from 130°C to 171°C (266°F to 340°F), depending on the grade and specific formulation. This high melting point allows polypropylene to maintain its structural integrity and dimensional stability under elevated temperatures.
Furthermore, polypropylene exhibits better dielectric properties compared to polyethylene. It has low electrical conductivity, making it an excellent electrical insulator. This characteristic is advantageous in applications where electrical insulation and non-conductivity are required.
In addition to its chemical resistance, polypropylene is lighter in weight compared to polyethylene, making it an attractive choice for applications where weight reduction is desirable. It also offers higher resistance to cracking, which enhances its durability and longevity in various environments and applications.
The monomer of polyethylene is ethylene, while the monomer of polypropylene is propylene.
In other words, in polymer chemistry, monomers are the building blocks that join together to form larger chains known as polymers. In the case of polyethylene, the monomer is ethylene. Ethylene is a simple hydrocarbon molecule consisting of two carbon atoms and four hydrogen atoms (C2H4). Through a process called polymerization, multiple ethylene monomers chemically bond together to create long chains of polyethylene.
On the other hand, for polypropylene, the monomer is propylene. Propylene is another hydrocarbon molecule with three carbon atoms and six hydrogen atoms (C3H6). Through polymerization, propylene monomers link together to form polypropylene chains.
Essentially, the difference in monomers between polyethylene and polypropylene is the type of hydrocarbon molecule that serves as the building block. This distinction in monomers contributes to the unique properties and characteristics exhibited by each polymer.
Polyethylene has a lower melting point compared to polypropylene.
The melting point of polyethylene typically ranges from around 105°C to 135°C (221°F to 275°F), depending on the specific grade and formulation. On the other hand, polypropylene has a higher melting point, ranging from approximately 130°C to 171°C (266°F to 340°F).
The difference in melting points is significant because it influences the thermal behavior and processing characteristics of these polymers. The lower melting point of polyethylene means that it can be easily melted and molded at lower temperatures compared to polypropylene. This property makes polyethylene more suitable for processes like blow molding, where the plastic is melted and shaped into hollow objects like bottles or containers.
In contrast, the higher melting point of polypropylene allows it to withstand higher temperature environments without losing its structural integrity. This makes polypropylene more suitable for applications that require higher heat resistance, such as microwave-safe containers or components used in hot-fill processes.
Understanding the melting points of polyethylene and polypropylene is crucial for selecting the appropriate material for specific applications. It ensures that the chosen polymer can withstand the intended processing conditions and the environmental factors it may encounter during its lifecycle.
Polypropylene is generally stiffer, more resistant to chemicals, and less stretchable than polyethylene.
Here are examples that illustrate the differences between polypropylene and polyethylene in terms of stiffness, chemical resistance, and stretchability:
-
Stiffness: Polypropylene is generally stiffer than polyethylene, meaning it has less flexibility and is more rigid. This characteristic makes polypropylene suitable for applications that require structural integrity and dimensional stability. For example:
-
Automotive Components: Polypropylene is commonly used in the manufacturing of automotive parts, such as bumpers, interior trim panels, and instrument panels. Its stiffness helps these components maintain their shape and withstand mechanical stress.
-
Packaging Crates: Polypropylene is used to create rigid packaging crates for shipping and storage. The stiffness of polypropylene ensures that the crates can support heavy loads without deforming or collapsing.
-
Chemical Resistance: Polypropylene exhibits higher resistance to a wide range of chemicals compared to polyethylene. It can withstand exposure to various substances without significant degradation or damage. Examples include:
-
Chemical Storage Containers: Polypropylene is commonly used for storing and transporting chemicals, such as acids, solvents, and corrosive substances. Its chemical resistance prevents the container from deteriorating or reacting with the contents.
-
Laboratory Equipment: Polypropylene is employed in the production of laboratory equipment, such as beakers, test tubes, and pipette tips. Its resistance to a variety of chemicals ensures that the equipment remains unaffected during experiments or chemical reactions.
-
Stretchability: Polyethylene is generally more stretchable than polypropylene, meaning it has higher elongation or flexibility. This property makes polyethylene suitable for applications that require stretchability or elasticity. Examples include:
-
Plastic Bags: Polyethylene is extensively used in the production of plastic bags, including grocery bags, garbage bags, and various packaging bags. Its stretchability allows the bags to accommodate different shapes and sizes of items.
-
Stretch Films: Polyethylene stretch films are commonly used for wrapping and securing pallets during transportation. The stretchability of polyethylene allows the film to tightly conform to the shape of the pallet, providing stability and protection to the stacked goods.
These examples highlight how the stiffness, chemical resistance, and stretchability of polypropylene and polyethylene contribute to their respective applications in various industries and product categories.
Are both polyethylene and Polypropylene recyclable?
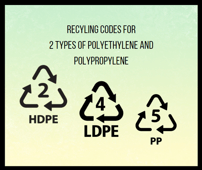
Yes, both polyethylene and polypropylene are recyclable. Polyethylene is commonly identified with the recycling code "2" (HDPE - High-Density Polyethylene) and "4" (LDPE - Low-Density Polyethylene). Polypropylene is identified with the recycling code "5" (PP - Polypropylene). These codes help in sorting and recycling plastics efficiently.
In Conclusion: Understanding the distinctions between polyethylene and polypropylene helps in selecting the appropriate material for specific applications, considering factors like transparency, temperature resistance, electrical properties, and rigidity.
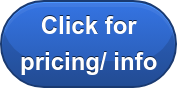
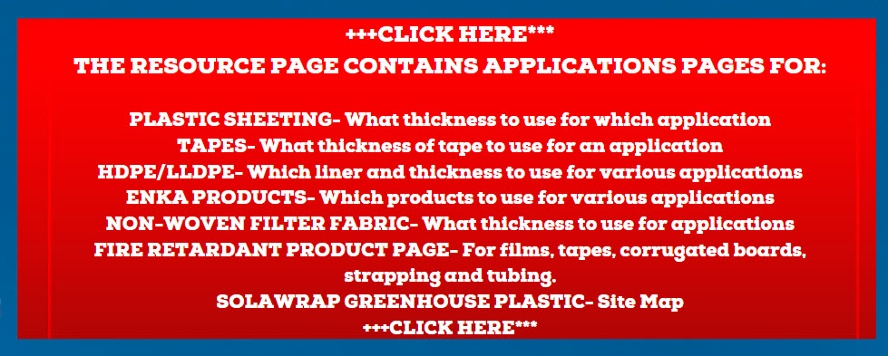