What is Strapping?
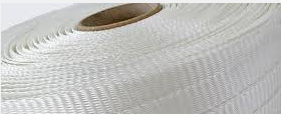
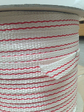
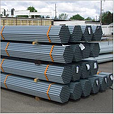
Strapping has many names for the same product. It is called, "woven cord strapping", "woven polyester strapping", "woven poly strapping", "polyester cord strapping", and even "hand tie poly cord". What do we mean when we speak of “strapping”? Strapping is defined for this article as a flat material that is most often used for bundling and banding items to hold them in place. Strapping is also used to fasten or reinforce products. Strapping is used in agriculture, construction, shipping, packaging, lumber yards, and just about anywhere items need to be held together (contained) with something more than twine or string. There are different kinds of strapping- Steel strapping, plastic strapping, woven poly strapping.
Steel Strapping
Steel strapping is the winner when you talk about time on the market. From what we can find, steel strapping, also called “steel banding”, was introduced in the late 19th century. Today steel strapping is made by “rolling” the metal to literally flatten it. There are two types of rolled metal- “hot rolling” and “cold rolling”. If the temperature of the metal is above its recrystallization temperature, then the process is known as hot rolling. If the temperature of the metal is below its recrystallization temperature, the process is known as cold rolling. Steel strapping also comes in a variety of thicknesses and widths as well as variations in the grade of steel. The industry refers to the strengths as “regular duty” and “High Tensile”. Break strengths can go as high as 12,500 pounds. Regular Duty (RG) strapping is usually a low carbon steel strapping produced for low to medium duty applications, e.g., package reinforcement, unitizing, bundling palletizing and box closure. Regular duty steel strapping can be used in manual and pneumatic tools, as well as automatic steel strapping heads. High Tensile (HT): A high carbon steel strapping that is heat treated to produce a product which combines high strength and elongation (stretch) for shock resistance. Typical applications are unitizing compressed fiber bales, securing heavy steel coils and open top rail car and trailer loading. High Tensile strapping provides more footage per coil than heavy duty sizes of comparable break strength.
Steel is used for holding heavy loads where strength and minimal stretch are desired. Steel strapping also has different surface finishes. Some of the finishes include paint, paint and wax, bluing or zinc (galvanized) and wax. Galvanized steel is a process where the steel is “hot-dipped” in molten zinc to prevent corrosion.
While steel banding had its advantages, it also has its disadvantages. Some steel strapping if left untreated has the potential to rust, and thus stain the cargo which it is touching. It can also tear and/or scratch the cargo. If a steel band is cut from a bundle in a careless manner, the steel band most likely will lash and cause deep bounds. In addition, since steel banding coil weigh so much when compared to other banding materials, many people also get injured from loading these coils into a dispenser. Another consideration is the cost. Not only is steel expensive, but with fluctuating markets, budgeting is erratic.
Steel strapping is a less than ideal solution if the bundle should settle and become smaller. Steel banding will remain the same size and will no longer hold the cargo securely. The best time to use steel is when the pallet weights are excessive- 4000 pounds or more. If the load has sharp edges, is a non-compressed bundle, and you need the strap to be the package security.,
PLASTIC STRAPPING
There are three types of “plastic strapping”. Let’s take a look at each one; polypropylene, polyester, and nylon. So to quickly answer the question, yes, plastic strapping and poly strapping are one in the same. It is how they are manufactured that makes the difference.
Polypropylene strapping is considered a light to medium duty strap. This economical option is best for light duty palletizing, unitizing, carton closing and bundling. It is used in all semi-automatic strappers and nearly all standalone arch machines It is manufactured in various thicknesses, widths and polymer variations. Often it is embossed or printed. Polypropylene strapping is most commonly used. It is light and easy to apply and recycle. It has high elongation and elongation recovery, but low retained tension. Polypropylene strapping will lose about 50% of the applied tension within one hour, and that this tension loss is accelerated with increases in ambient temperature. If the bundle is something that can take up the slack, then this is not such a huge issue. If however the bundle is a solid brick such as a block of concrete, the slack will be problematic. Additionally, the sun and its UV rays are an enemy to polypropylene strapping. UV degradation can occur is the bundle is left outside in the sun. If the polypropylene strapping has been treated with UV inhibitors, then the strapping will fare better in the sun.
Polypropylene strapping can be printed which has marketing advantages for companies. The printing can also offer security. It is available in manual and machine grade. It can be sealed with buckles, seals, heat seals or friction welds. Polypropylene can be used for loads up to 2000 pounds, has moderate settling, is light weight.
Nylon strap has the greatest “specific strength” of the three plastics. Specific strength is defined as a material's strength (force per unit area at failure) divided by its density. It is also known as the strength-to-weight ratio or strength/weight ratio. In fiber or textile applications, tenacity is the usual measure of specific strength. While nylon is strong, its high price is a deterrent in today’s market. Nylon has been replaced by polyester.
Polyester strapping is the third type of plastic strapping. Polyester and nylon are the strongest plastic strapping products and are used as an alternative to steel in some applications. Polyester strapping can be woven or nonwoven. The nonwoven strap referred to as “composite straps’ consist of polyester filaments in a straight line that are encased in a polymer. Woven Polyester strapping is even stronger than the composite straps due to the filaments being weaved together.Woven polyester strapping can be applied using a ratcheting tensioner and a high joint efficient buckle.
Why is woven polyester strapping so popular?
- Polyester strapping retains excellent tension on rigid loads. It also has excellent recovery properties to help a load absorb impact without the strap breaking.
- Woven poly strapping won’t stain or rust like steel strapping can.
- The soft nature of poly strapping won’t damage the bundle being secured.
- The polyester strapping won’t snap or break causing injury.
- It is lightweight and much easier to work with and dispose of.
- Both woven polyester and the composite strapping maintains its shape even under rigorous weather conditions.
- Resistant to high temperatures, ultraviolet rays and moisture.
- Polyester strapping can be printed.
Summary
Comparing steel, polyester, nylon and polypropylene strapping we find:
Steel: Strongest, most expensive, least impact resistant, and lowest moisture resistance.
Polyester: Lowest notch sensitivity, second lowest cost behind polypropylene, best impact,moisture and environmental resistance.
nylon: It falls in the middle of steel and polypropylene. It is second in cost to steel, had the highest elongation, but adequate moisture and environmental resistance.
Polypropylene: Least expensive, lowest break strength, and great environmental resistance.
The key to selecting the strapping is to know your load characteristics and the strapping attributes.Click to edit your new post...
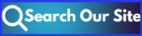