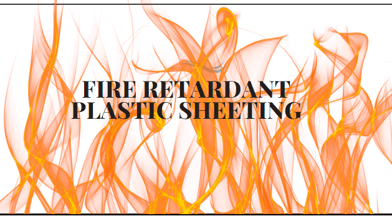
Fire retardant plastic sheeting plays a crucial role in fire safety by preventing the spread of flames and reducing the risk of fire-related accidents. Its ability to resist ignition and slow down the burning process makes it an essential component in protecting lives and property.
When it comes to fire safety, every precaution must be taken to protect lives and property. One essential component in this regard is fire retardant plastic sheeting. Its flame resistance properties make it an indispensable tool in preventing the spread of flames and reducing the risk of fire-related accidents.
Fire retardant plastic sheeting is specifically designed to resist ignition and slow down the burning process. This is achieved through the incorporation of flame retardant additives during the manufacturing process. These additives work by releasing flame-inhibiting gases when exposed to heat or flames, thereby suppressing the combustion process.
One of the key advantages of fire retardant plastic sheeting is its ability to self-extinguish. Unlike regular plastic, which can continue to burn and contribute to the spread of flames, fire retardant plastic sheeting will stop burning once the ignition source is removed. This not only prevents the fire from spreading further, but it also reduces the release of toxic fumes and smoke, which can be equally dangerous to human health.
In addition to its flame resistance properties, fire retardant plastic sheeting also offers other benefits. It is highly durable and resistant to impact, making it suitable for use in high-risk areas where accidents are more likely to occur. It is also resistant to chemicals and UV rays, ensuring its longevity and effectiveness in various environments.
Fire retardant plastic sheeting finds applications in a wide range of industries and settings. It is commonly used in construction sites, where it acts as a temporary barrier to contain potential fires
2. Preventing the Spread of Flames
Fire retardant plastic sheeting plays a crucial role in preventing the spread of flames and reducing the risk of fire-related accidents. Its ability to resist ignition and slow down the burning process makes it an essential component fire safety.
One of the key advantages of fire retardant plastic sheeting is its flame resistance properties. It is specifically designed to resist ignition and suppress the combustion process. This is achieved through the incorporation of flame retardant additives during the manufacturing process. When exposed to heat or flames, these additives release flame-inhibiting gases, preventing the spread of flames.
Unlike regular plastic, which can continue to burn and contribute to the spread of flames, fire retardant plastic sheeting will self-extinguish once the ignition source is removed. This not only prevents the fire from spreading further but also reduces the release of toxic fumes and smoke, which can be equally dangerous to human health.
In addition to its flame resistance properties, fire retardant plastic sheeting offers other benefits. It is highly durable and resistant to impact, making it suitable for use in high-risk areas where accidents are more likely to occur. It is also resistant to chemicals and UV rays, ensuring its longevity and effectiveness in various environments.
Fire retardant plastic sheeting finds applications in a wide range of industries and settings. It is commonly used in construction sites, where it acts as a temporary barrier to contain potential fires. It can also be found in transportation, manufacturing, and healthcare industries, where fire safety is of utmost importance
How effective is fire retardant plastic sheeting at protecting surfaces?
Fire retardant plastic sheeting can be highly effective at protecting surfaces from potential fire damage. The primary purpose of fire retardant plastic sheeting is to delay or prevent the spread of flames and heat. It acts as a barrier, shielding surfaces from direct contact with fire and reducing the risk of ignition.
The effectiveness of fire retardant plastic sheeting depends on several factors, including the quality of the material, its thickness, and its installation. High-quality fire retardant plastic sheeting is typically made from durable that have been treated with fire-resistant chemicals. These chemicals can help to slow down the combustion process and prevent the plastic sheeting from catching fire easily.
The thickness of the plastic sheeting also plays a role in its effectiveness. Thicker sheets tend to provide better protection as they offer more insulation and are less likely to melt or burn. Thinner sheets may still provide some level of protection, but they are generally not as reliable.
Proper installation is crucial for maximizing the effectiveness of fire retardant plastic sheeting. It should be securely fastened and cover the entire surface area that needs protection. Any gaps or openings can compromise its ability to prevent fire from spreading. Additionally, it is important to ensure that the sheeting is installed in a way that does not obstruct essential safety features, such as exits or sprinkler systems.
While fire retardant plastic sheeting can be effective at protecting surfaces, it is important to note that it is not a foolproof solution. It can provide temporary protection
What types of fire retardant plastic sheeting are available?
Fire retardant plastic sheeting is available in a variety of types, each offering different levels of fire resistance and durability. Here are some common types of fire retardant plastic sheeting:
1. Flame Retardant Polyethylene (PE) Sheeting: This type of plastic sheeting is made from polyethylene, a commonly used plastic material. It has been treated with fire retardant additives to reduce its flammability. Flame retardant PE sheeting is lightweight, flexible, and provides a basic level of fire resistance.
2. Fire Retard Sheeting: PVC sheeting is another popular choice for fire retardant applications. PVC is naturally flame resistant, but fire retardant additives can further enhance its fire resistance properties. Fire retardant PVC sheeting is durable, weatherproof, and commonly used for construction and industrial purposes.
3. Fire Retardant Polypropylene (PP) Sheeting: Polypropylene sheeting is known for its excellent chemical resistance and high tensile strength. Fire retardant PP sheeting is treated with additives that inhibit the spread of flames and reduce smoke generation. It is often used in applications where fire safety is critical, such as hospitals and laboratories.
4. Fire Retardant Polycarbonate (PC) Sheeting: Polycarbonate sheeting offers superior impact resistance and transparency. Fire retardant polycarbonate sheeting is treated with additives that provide flame retardancy while maintaining its desirable physical properties. Itis commonly used in applications where both fire safety and visibility are important, such as in windows or partitions.
These are just a few examples of the types of fire retardant plastic sheeting available. The specific type of sheeting chosen will depend on the requirements of the application and the level of fire resistance needed. It is important to consult with a knowledgeable supplier or manufacturer to determine the most suitable type of fire retardant plastic sheeting for your specific needs.
How durable is fire retardant plastic sheeting?
Fire retardant plastic sheeting is designed to provide protection against fire and is commonly used in various industries and applications. The durability of fire retardant plastic sheeting depends on several factors, including the quality of the material, its thickness, and the specific requirements of the intended use.
Fire retardant plastic sheeting is typically made from polyethylene, which is inherently resistant to fire. However, to enhance its fire resistance properties, additional additives and treatments are incorporated into the plastic during the manufacturing process.
These additives and treatments help to increase the sheeting's resistance to ignition, reduce its flammability, and slow down the spread of flames. They also help to minimize the release of toxic gases and smoke, which can be potentially harmful during a fire.
The durability of fire retardant plastic sheeting can be evaluated based on its compliance with industry standards and certifications. Look for products that meet recognized fire safety standards such as the National Fire Protection Association (NFPA) or Underwriters Laboratories (UL) standards. These certifications indicate that the sheeting has undergone rigorous testing and meets specific fire safety requirements.
In addition to fire resistance, the durability of plastic sheeting is also influenced by other factors such as UV resistance, tear resistance, and resistance to environmental factors like moisture and chemicals. It is important to choose fire retardant plastic sheeting that is specifically designed for the intended application and the environmental conditions it will be exposed to.
Is White the Only Color For FR Plastic Sheeting?
No, white is not the only color available for fire retardant plastic sheeting. Fire retardant plastic sheeting is available in a variety of colors, including clear, black, and various shades of gray. The choice of color depends on the specific needs and requirements of the application.
Clear fire retardant PVC is often used when visibility is important, such as in windows or partitions. It allows light to pass through while still providing fire protection. Black fire retardant plastic sheeting is commonly used for applications where light blockage is desired, such as in theaters or photography studios. Gray fire retardant plastic sheeting is a neutral color that is often chosen for general purposes.
When selecting the color of fire retardant plastic sheeting, it is important to consider factors such as the desired level of visibility, light transmission, and aesthetic preferences. Additionally, it is important to ensure that the chosen color meets the necessary fire safety standards and certifications.
Is Flame Retardant Plastic Sheeting Actually “Fireproof”?
No, flame retardant plastic sheeting is not "fireproof." While flame retardant additives and treatments are incorporated into the plastic during the manufacturing process to enhance its fire resistance properties, they do not make the sheeting completely immune to fire.
Fire retardant plastic sheeting is designed to slow down the spread of flames, reduce its flammability, and minimize the release of toxic gases and smoke during a fire. It provides a basic level of fire resistance and can help prevent the spread of flames to other areas. However, it is still important to take proper fire safety precautions and follow appropriate fire prevention measures when using fire retardant plastic sheeting.
To ensure the highest level of fire safety, it is crucial to choose fire retardant plastic sheeting that meets recognized industry standards and certifications, such as those set by the National Fire Protection Association (NFPA) or Underwriters Laboratories (UL). These certifications indicate that the sheeting has undergone rigorous testing and meets specific fire safety requirements.
In summary, while flame retardant plastic sheeting provides a level of fire resistance and can help prevent the spread of flames, it is not considered "fireproof." It is important to use fire retardant plastic sheeting in conjunction with proper fire safety measures for the best protection against fire-related accidents.
Does The FR Plastic Come With Printing?
Yes, flame retardant plastic sheeting can come with printing. Depending on the manufacturer or supplier, fire retardant plastic sheeting can be customized with various types of printing, such as logos, safety warnings, or specific instructions. This can be useful for applications where clear communication or branding is necessary. However, it is important to ensure that the printing does not compromise the fire resistance properties of the sheeting. When considering printed fire retardant plastic sheeting, it is advisable to consult with the manufacturer or supplier to ensure that the printing does not affect the sheeting's fire safety certifications and compliance with industry standards.
What is meant by “Extrusion Laminate”?
“Extrusion laminate” refers to a manufacturing process used to create fire retardant plastic sheeting. During extrusion lamination, multiple layers of plastic are fused together using heat and pressure. This results in a strong and durable sheeting that is resistant to fire.
In the extrusion lamination process, a molten plastic material is extruded through a die, which forms a continuous sheet. This sheet is then combined with other layers of plastic, such as a fire retardant layer, to create a laminate. The layers are bonded together under high pressure and cooled to solidify the sheeting.
Extrusion lamination is commonly used in the production of fire retardant plastic sheeting because it allows for the incorporation of different materials with specific properties. For example, a fire retardant layer can be added to enhance the sheeting's fire resistance, while other layers can provide UV resistance or tear resistance.
The extrusion lamination process ensures that the different layers of the laminate are securely bonded together, creating a durable and long-lasting fire retardant plastic sheeting. This process also allows for customization, such as printing or adding other features to meet specific application requirements.
Overall, extrusion lamination is a crucial step in the manufacturing of fire retardant plastic sheeting, as it ensures the sheeting's durability and enhances its fire resistance properties.
Does Flame Retardant Poly Film Come in a 6 mil Thickness?
Yes, flame retardant poly film does come in a 6 mil thickness. The thickness of the film refers to the gauge or thickness of the plastic sheeting. The higher the mil measurement, the thicker and more durable the film will be.
6 mil flame retardant poly film is commonly used in construction and industrial applications where a higher level of fire resistance and durability is required. provides a strong barrier against flames and helps prevent the spread of fire. Additionally, the thicker film is more resistant to tears and punctures, making it suitable for applications where it may be exposed to rough conditions or heavy use.
When selecting flame retardant poly film, it is important to consider the specific requirements of your application and consult with a knowledgeable supplier or manufacturer. They can help you determine the appropriate thickness and type of film that will best meet your needs.
Overall, using a 6 mil thickness flame retardant poly film can provide enhanced fire protection and durability in various industries and settings.
Yes, fire retardant corrugated sheets can be used to create temporary walls. Fire retardant corrugated sheets are typically made from materials such as polypropylene or polycarbonate that have been treated with fire retardant additives to reduce flammability. These sheets are lightweight, durable, and easy to install, making them an ideal choice for creating temporary walls in various settings.
Fire retardant corrugated sheets can be used in construction sites, industrial facilities, and other locations where temporary partitions or barriers are needed to separate different areas. They can help to prevent the spread of fire and provide added safety in case of emergencies.
To create temporary walls using fire retardant corrugated sheets, the sheets can be attached to a frame or mounted directly onto existing structures. The sheets can be easily cut to size and can be joined together using connectors or adhesive tapes.
It is important to ensure that the sheets are properly installed and securely fastened to create a stable and effective temporary wall. Any gaps or openings should be sealed to prevent the spread of fire. Additionally, the temporary walls should not obstruct essential safety features, such as exits or sprinkler systems.
When using fire retardant corrugated sheets to create temporary walls, it is crucial to follow all safety guidelines and regulations. Consulting with a knowledgeable supplier or manufacturer can help ensure that the correct type and thickness of fire retardant corrugated sheets are chosen for the specific application and level of fire resistance required.
Antistatic fire retardant plastic sheeting is a specialized type of fire retardant plastic sheeting that is designed to prevent the buildup of static electricity. Static electricity can pose a significant risk in certain environments, as it can ignite flammable materials and potentially cause fires or explosions.
Antistatic fire retardant plastic sheeting is made with materials that have antistatic properties, which means they can dissipate or neutralize static electricity. This helps to minimize the risk of sparks or electrical discharge that could ignite a fire.
The fire retardant properties of this type of sheeting are achieved through the incorporation of fire retardant additives or treatments, similar to other types of fire retardant plastic sheeting. These additives or treatments help to reduce the flammability of the sheeting and slow down the spread of flames.
Antistatic fire retardant plastic sheeting is commonly used in industries where static electricity can be a concern, such as electronics manufacturing, cleanrooms, and explosive or hazardous material handling facilities. It provides an additional layer of safety by combining both antistatic and fire retardant properties.
When choosing antistatic fire retardant plastic sheeting, it is important to consider the specific requirements of the application and the level of fire resistance needed. Consulting with a knowledgeable supplier or manufacturer is recommended to ensure that the selected sheeting meets the necessary standards and regulations for the intended use.
In summary, antistatic fire retardant plastic sheeting is a specialized type of sheeting that combines
Are there different grades of fire retardant plastic sheeting?
Yes, there are different grades of fire retardant plastic sheeting available in the market. These grades are determined based on the level of fire resistance and performance they offer.
Fire retardant plastic sheeting is designed to inhibit the spread of flames and reduce the risk of fire hazards. It is commonly used in various applications such as construction, agriculture, and industrial settings where fire safety is a concern.
The different grades of fire retardant plastic sheeting typically correspond to the level of fire resistance they provide. These grades are often classified using industry standards and certifications to ensure the quality and performance of the product.
One common classification system used for fire retardant plastic sheeting is the flame spread rating. This rating measures how quickly flames can spread across the surface of the material. The lower the flame spread rating, the better the fire resistance of the plastic sheeting.
Another classification system is based on specific fire safety standards, such as the National Fire Protection Association (NFPA) codes. These standards specify different levels of fire resistance and performance requirements for different applications.
It is important to select the appropriate grade of fire retardant plastic sheeting based on the specific requirements of your application. Factors such as the type of environment, fire safety regulations, and intended use should be taken into consideration.
When purchasing fire retardant plastic sheeting, it is recommended to look for reputable suppliers who can provide documentation and certifications to verify the grade and performance of the product. These certifications may include testing reports, compliance with industry standards,and fire safety certifications.
Some common grades of fire retardant plastic sheeting include:
1. Class A: This grade offers the highest level of fire resistance and is suitable for applications where strict fire safety regulations are in place. Class A fire retardant plastic sheeting typically has a low flame spread rating and meets the highest performance requirements.
2. Class B: This grade provides a moderate level of fire resistance and is commonly used in applications where fire safety is a concern but not as strict as Class A. Class B fire retardant plastic sheeting has a higher flame spread rating compared to Class A, but still offers reliable fire protection.
3. Class C: This grade offers the lowest level of fire resistance and is suitable for applications where fire safety is not a major concern. Class C fire retardant plastic sheeting typically has a higher flame spread rating and may not meet the strictest fire safety regulations.
It is important to note that fire retardant plastic sheeting should be chosen based on the specific requirements of your application. Factors such as the type of environment, fire safety regulations, and intended use should be taken into consideration.
When selecting fire retardant plastic sheeting, it is recommended to work with reputable suppliers who can provide documentation and certifications to verify the grade and performance of the product. This ensures that you are purchasing a reliable and high-quality product that meets your fire safety needs.
In conclusion, there are different grades of fire retardant plastic sheeting available, each offering varying levels of fire
What types of fire retardant plastic sheeting are available?
Fire retardant plastic sheeting is an essential material for various applications where fire safety is a concern. It is widely used in construction provide a barrier against flames and smoke. There are several types of fire retardant plastic sheeting available, each offering unique properties and advantages. In this article, we will discuss the most common types of fire retardant plastic sheeting.
1. Polyethylene (PE) Fire Retardant Plastic Sheeting: Polyethylene is a popular choice for fire retardant plastic sheeting due to its excellent balance of strength and flexibility. PE sheeting is treated with fire-retardant additives during the manufacturing process, which enhance its resistance to flames and reduce smoke emission. These additives work by releasing flame-inhibiting gases when exposed to heat, thus slowing down the spread of fire. PE fire retardant sheeting is commonly used in temporary enclosures, construction sites, and as a vapor barrier in crawl spaces.
2. Polyvinyl Chloride (PVC) Fire Retardant Plastic Sheeting: PVC is another widely used material for fire retardant plastic sheeting. It has excellent fire resistance properties and is self-extinguishing, meaning it does not support combustion once the source of ignition is removed. PVC fire retardant sheeting is highly durable, weather-resistant, and can withstand extreme temperatures. It is commonly used in indoor and outdoor applications, such as tarpaulins, protective coverings, and containment barriers.
3. Polycarbonate Fire Retardant Plastic Sheeting: Polycarbonate is a strong and impact-resistant material that offers excellent fire resistance. It has a high melting point and does not release toxic gases when exposed to flames. Polycarbonate fire retardant sheeting is commonly used in applications where high impact strength and fire protection are required, such as safety glazing, roofing, and industrial enclosures.
4. Acrylic Fire Retardant Plastic Sheeting: Acrylic is known for its transparency and optical clarity, making it a popular choice for fire retardant plastic sheeting in applications where visibility is important. Acrylic fire retardant sheeting offers good fire resistance and does not release toxic fumes when exposed to flames. It is commonly used in windows, skylights, and protective barriers.
5. Polypropylene (PP) Fire Retardant Plastic Sheeting: Polypropylene is a versatile material with good fire resistance properties. PP fire retardant sheeting is lightweight, flexible, and offers excellent chemical resistance. It is commonly used in applications such as temporary partitions, packaging, and industrial enclosures.
When selecting the type of fire retardant plastic sheeting for your application, it is important to consider factors such as the level of fire resistance required, environmental conditions, and specific performance requirements. Working with reputable suppliers who can provide documentation and certifications is crucial to ensure you are purchasing a reliable and high-quality product that meets your fire safety needs.
Is fire retardant plastic sheeting easy to install?
Fire retardant plastic sheeting is relatively easy to install. The process can be completed by following a few simple steps.
Firstly, gather all the necessary tools and materials. These may include the fire retardant plastic sheeting, measuring tape, utility knife, adhesive or fasteners, and a ladder or scaffolding if needed.
Next, measure the area where the sheeting will be installed. Take accurate measurements to ensure the sheeting fits properly and covers the desired area.
After measuring, cut the plastic sheeting to the appropriate size using a utility knife. Ensure that the edges are clean and straight for a proper fit.
If needed, apply adhesive to the back of the sheeting or use fasteners to secure it in place. Adhesive can be applied directly to the surface or to the edges of the sheeting, depending on the manufacturer's instructions. Fasteners such as nails or staples can be used to secure the sheeting to a wooden surface.
Carefully apply the sheeting to the designated area, making sure it is aligned correctly. Smooth out any wrinkles or air bubbles to ensure a tight fit.
If installing the sheeting on a vertical surface, use a ladder or scaffolding to reach higher areas safely.
Once the sheeting is installed, inspect it for any gaps or loose areas. If any are found, secure them properly to ensure the sheeting provides effective fire retardant properties.
In conclusion, fire retardant plastic sheeting is relatively easy to install. By following the steps
How long does fire retardant plastic sheeting last?
Fire retardant plastic sheeting typically has a lifespan of 2 to 5 years, depending on various factors such as the quality of the material, exposure to sunlight, and environmental conditions. It is important to note that the effectiveness of fire retardant properties may diminish over time, especially if the sheeting is subjected to frequent wear and tear or prolonged exposure to ultraviolet (UV) rays.
To the longevity and effectiveness of fire retardant plastic sheeting, it is recommended to store it in a cool, dry place when not in use. Additionally, regular inspections should be conducted to check for any signs of damage or degradation. If any defects or deterioration are noticed, it is advisable to replace the sheeting promptly to maintain its fire retardant capabilities.
It is worth mentioning that manufacturers may provide specific guidelines or recommendations regarding the lifespan of their fire retardant plastic sheeting products. Following these guidelines can help maximize the durability and functionality of the sheeting. Furthermore, compliance with local regulations and fire safety standards is crucial to ensure the appropriate and safe use of fire retardant plastic sheeting.
In conclusion, fire retardant plastic sheeting can last between 2 to 5 years, but its lifespan may vary depending on several factors. Regular inspections and adherence to manufacturer guidelines are vital to maintain the sheeting's fire retardant properties and ensure its effectiveness in fire safety applications.
Are there different grades of fire retardant plastic sheeting?
Yes, there are different grades of fire retardant plastic sheeting available in the market. These grades are determined by the level of fire resistance they offer and the specific standards they meet.
Fire retardant plastic sheeting is designed to slow down or prevent the spread of fire by inhibiting the combustion process. The level of fire resistance provided by a particular grade of fire retardant plastic sheeting is determined by its ability to meet certain fire safety standards.
There are several fire safety standards that fire retardant plastic sheeting can conform to, such as the National Fire Protection Association (NFPA) standards or the Underwriters Laboratories (UL) standards. Each standard has its own set of requirements for fire resistance and has different grades or classifications for fire retardant materials.
These grades or classifications are often denoted by specific codes or symbols indicating the level of fire resistance. For example, Class A fire retardant plastic sheeting is the highest level of fire resistance and meets the most stringent requirements. Class B and Class C are lower levels of fire resistance, with Class C being the lowest.
It's important to note that the specific requirements and classifications may vary depending on the country or region. Therefore, it is crucial to consult the local fire safety regulations and standards to ensure compliance with the appropriate grade of fire retardant plastic sheeting for a particular application.
In conclusion, yes, there are different grades of fire retardant plastic sheeting available, and the choice of grade depends on the desired level of fire resistance
Fire retardant plastic sheeting is highly effective at protecting surfaces from fire damage. This material is specifically designed to slow down or prevent the spread of fire by reducing its heat and oxygen supply. The fire retardant additives in the plastic sheeting help to resist ignition and inhibit the combustion process.
One of the key advantages of fire retardant plastic sheeting is its ability to create a barrier between the fire and the protected surface. When exposed to heat or flame, the plastic sheeting undergoes a chemical reaction that forms a protective layer of carbon char. This layer acts as an insulator, reducing heat transfer and preventing the fire from reaching the surface underneath.
Additionally, fire retardant plastic sheeting is typically self-extinguishing, meaning it will stop burning once the flame source is removed. This characteristic ensures that the fire does not sustain or continue to spread, providing valuable time for evacuation or fire suppression efforts.
Fire retardant plastic sheeting is commonly used in various industries and applications where fire protection is critical. It is often employed in construction sites, remodeling projects, and temporary installations to cover and safeguard surfaces such as walls, floors, furniture, or equipment. It can also be used in commercial settings, such as theaters, event venues, or warehouses, to create fire-resistant barriers and partitions.
It is important to note that the effectiveness of fire retardant plastic sheeting can vary depending on factors such as the thickness and quality of the material, the specific fire retardant additives used, and the duration
In conclusion, fire retardant plastic sheeting plays a crucial role in fire safety by preventing the spread of flames and reducing the risk of fire-related accidents. Its flame resistance properties, durability, and resistance to impact, chemicals, and UV rays make it an effective solution for various industries and settings. By choosing the right type of fire retardant plastic sheeting and ensuring proper installation, surfaces can be effectively protected from potential fire damage.
In Summary Fire Retardant Plastic is the safe choice.
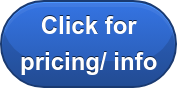
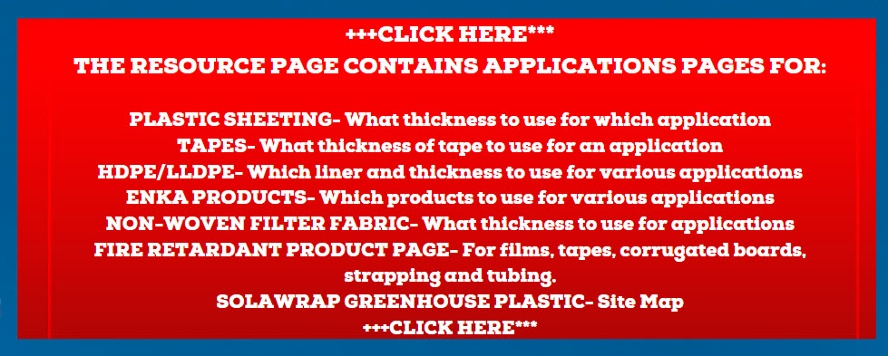