Temporary protective film for renovation projects
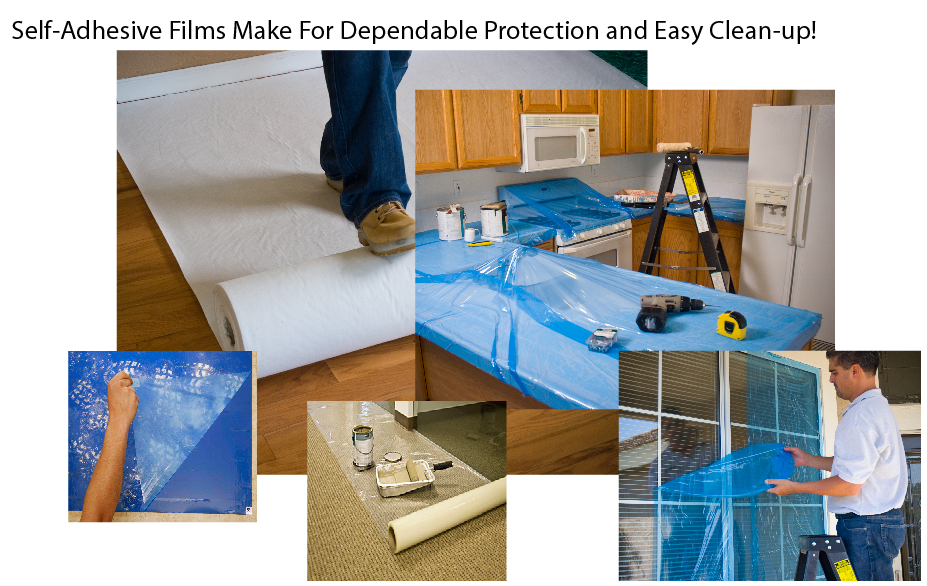
Embarking on a renovation project can be exciting, but it often comes with the hassle of protecting surfaces from damage and mess. Enter self-adhesive plastic film – a game-changer in the world of remodeling. Let's explore the effectiveness of this innovative solution and its various applications.
Adhesive Plastic Film for Countertop Protection During Remodeling: Protecting countertops during renovations is essential to maintain their pristine condition. Adhesive plastic film offers a reliable solution, effectively shielding countertops from scratches, stains, and spills. Its adhesive backing ensures secure coverage, preventing shifting or peeling during the remodeling process.
Introducing Countertop PlasticTM – a 3 mil Blue self-adhesive Polyethylene film specially engineered for countertop surfaces. Designed to provide scratch protection from fabrication to installation and beyond, this flexible plastic sheeting adheres securely, ensuring countertops remain pristine throughout the renovation process.
Countertop PlasticTM Adheres to Surfaces Including:
- Granite
- Tile
- Corian®
- Zodiac®
- Marble
- Quartz
- Soapstone
- Compac Marmol & Quartz
- Glass
- Concrete
- Formica®
- Swanstone
- Caesarstone
- Wilsonart Earthstone
- Gibraltar & Laminates ...and many other Acrylic and Resin countertop surfaces.
Key Features:
- Offers protection during fabrication, shipping, delivery, installation, and post-installation.
- Water-based adhesive system ensures strong adhesion without leaving residue.
- Available in various sizes and custom options to meet specific needs.
Carpet Plastic for Comprehensive Carpet Protection:
Experience the ultimate carpet protection with Carpet Plastic – a durable self-adhesive polyethylene film designed to safeguard carpets from construction activities and foot traffic. Whether used as a runner or for specific areas, this film withstands heavy use, ensuring carpets remain pristine until the renovation is complete.
Key Features:
- Blended LDPE/LLDPE construction for maximum strength and elongation.
- Water-based adhesives for secure adhesion and clean removal.
- Available in reverse wound rolls for easy application.
Granite Plastic for Surface Protection: Granite Plastic is your go-to solution for protecting granite surfaces from scratches, marring, and staining during fabrication and installation. With its smooth and clean release, this self-adhesive film ensures granite surfaces retain their pristine condition until the job is completed.
Key Features:
- Offers protection during fabrication, shipping, delivery, and installation.
- Available in two thicknesses: 2 mil Medium Tack and 3 mil Medium Tack.
Exploring Global Plastic Sheeting's Self-Adhesive Films: Global Plastic Sheeting offers a range of self-adhesive films tailored to specific renovation needs. From Carpet Plastic and Floor Plastic to Countertop Plastic and Marble Protection, their products are designed to provide superior surface protection during remodeling projects.
Benefits of Self-Adhesive Plastic Film:
- Ease of Installation: Quick and simple application saves time and effort.
- Surface Protection: Shields surfaces from scratches, stains, and damage.
- Clean Removal: Leaves no residue or adhesive marks upon removal, ensuring easy cleanup.
- Secure Adhesion: Adhesive backing prevents shifting or peeling, maintaining continuous protection.
- Versatile Applications: Suitable for various surfaces including carpets, countertops, floors, and more.
- Peace of Mind: Offers peace of mind knowing that surfaces are protected throughout the renovation process.
Considerations When Choosing Self-Adhesive Films: While self-adhesive films offer numerous benefits, it's essential to select high-quality products made in the USA to avoid potential issues such as residue or damage to surfaces. Global Plastic Sheeting's products prioritize quality and reliability, ensuring optimal performance and customer satisfaction.
In conclusion, self-adhesive plastic film is a valuable tool for simplifying and enhancing renovation projects. Whether protecting countertops, floors, or furniture, these innovative films offer unmatched convenience, protection, and peace of mind, making them a must-have for any remodeling endeavor.